AM structures are being used in a growing number of space system applications. Although AM can be attractive from design, schedule, and manufacturing perspectives, variability in material properties can be significant. This variability poses a concern that needs to be managed to ensure mission success.
A practical approach on how to adopt AM structures for national security space programs has been published. The degree of testing required is dependent on the type of hardware and is typically defined in existing standards. Verification may include performance, functional, vibration, shock, acoustic, thermal, pressure, and structural testing during qualification and acceptance. Verification requirements for AM hardware are no less than traditional hardware requirements, especially when new technology and manufacturing techniques are involved.
A flight-critical assessment provides insight into the consequences, including system failure, degraded performance, or instrumentation failure. System-level impacts could arise from contamination, impact damage, loss of conductivity, or loss of integrity or stiffness.
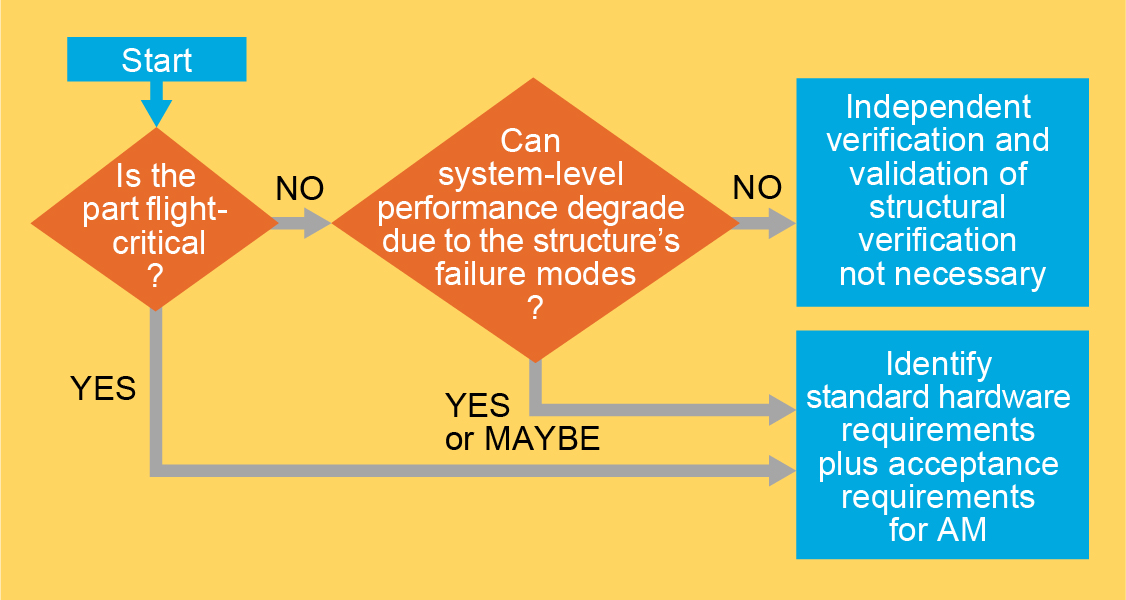
Understanding how a part’s failure modes can affect system-level performance is a key step in determining the extent of qualification and acceptance testing that is required for AM structures.
Similar to other process-sensitive hardware, proof testing of flight-critical AM structures is recommended to verify manufacturing and to ensure as-built hardware will survive a mission without failure or degradation. Less structural verification effort is required for nonflight-critical structures. The scope of structural verification activities should be based on the criticality of the AM part and the risk tolerance of the program.
As AM technology and process monitoring advance, AM hardware could become even more repeatable and robust compared to traditional manufacturing methods. If this future state is achieved, an update to test requirements would be warranted.
This study was published as TOR-2019-02060.
For more information, contact Brett E. Soltz, 310.336.6426, brett.e.soltz@aero.org.
This story appears in the December 2019 issue of Getting It Right, Collaborating for Mission Success.
Subscribe to Getting It Right
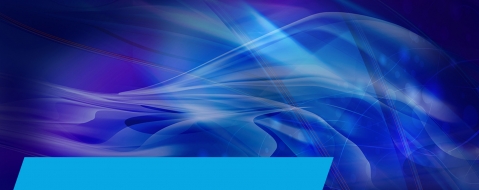