Deep inside a laboratory at The Aerospace Corporation's El Segundo campus, scientists are recreating the vacuum of space here on Earth.
Aerospace’s electric propulsion lab specializes in testing electric thrusters in space-like conditions, and they recently installed a new vacuum chamber that will enable them to test the newer, high-powered thrusters needed for future space exploration.
“This chamber adds not just to Aerospace’s testing capability, but adds to the world’s testing capability,” said Rostislav Spektor, Laboratory Manager in Electric Propulsion and Plasma Science. “When it becomes operational, it will be the best electric propulsion testing facility in the world.”
Why Electric Propulsion?
Everyone is familiar with the sight of fire and smoke pouring out of the bottom of a rocket using chemical propulsion.
Electric propulsion takes a different approach, harnessing electric energy to ionize gas into a plasma, which is accelerated out of the thruster through a combination of electric and magnetic forces.
Electric propulsion produces significantly less thrust than chemical propulsion but is much more efficient in terms of the amount of fuel used. It’s too weak to launch rockets through the atmosphere, but once in space, the lack of gravity allows electric propulsion thrusters’ true potential to shine.
“It’s the Tortoise and the Hare. Electric propulsion is slow but steady and chemical propulsion starts very fast, but runs out of steam quickly,” Spektor said.
Historically, electric propulsion has mostly been used for station-keeping of satellites. But its highly efficient nature opens up possibilities for long-distance space exploration missions with the small but constant thrust building up over time, accelerating the spacecraft to a very high velocity.
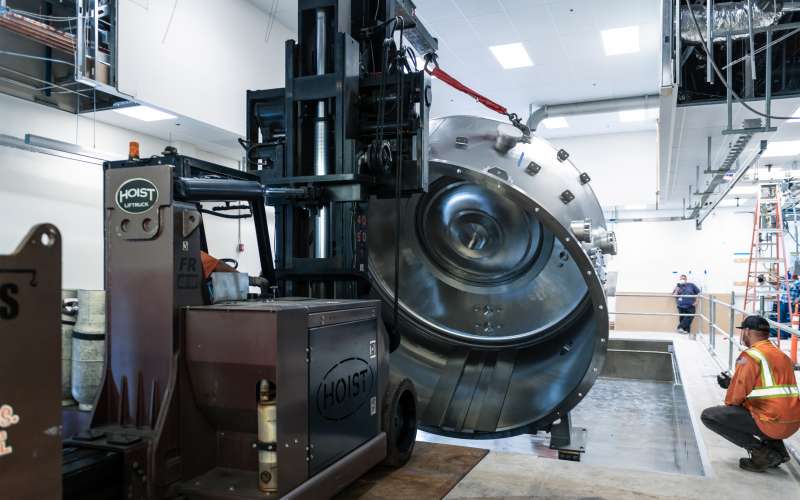
A Testing Powerhouse
In order to make those long journeys, however, scientists need to be able to trust that the thrusters will perform consistently and reliably over the duration of the mission.
That’s where electric propulsion vacuum chambers come into play. These school bus-sized devices are outfitted with a series of cryopumps that make the chamber very cold. When the pumps run, the air in the chamber sticks to the chamber sides, similar to condensation on a cold glass of water on a hot day. With the air gone, the chamber simulates the vacuum of space, and the team can place electric thrusters inside for testing.
“Electric propulsion devices perform differently in space than they do on Earth. The relationship isn’t linear, which can make predicting exactly how it will perform difficult,” said Spektor. “The closer you are to test-as-you-fly conditions, the closer you are to measuring performance you would expect in orbit.”
The new chamber, 14 ft in diameter and 30 ft long, is considerably larger than the lab’s older 8-foot diameter chamber, which means it has more room for cryopumps. The Aerospace team considered buying commercial pumps, but in the end decided to design their own pumping system to ensure optimal performance.
The chamber body was delivered in four segments over the course of a week and then bolted together. The custom-designed cryopump system will be installed over the next six months, followed by the diagnostic system.
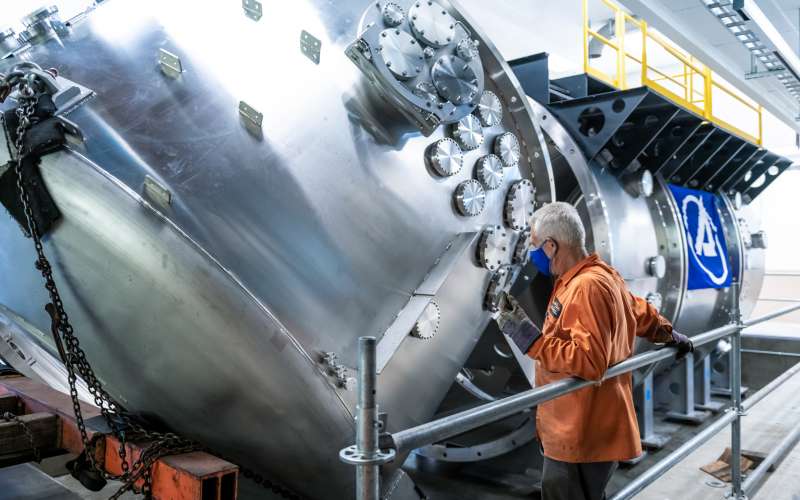
End-to-End Electric Propulsion Testing
As a federally-funded research and development center (FFRDC), Aerospace is not allowed to produce flight hardware that could compete with commercial companies.
Instead, Aerospace provides end-to-end testing of electric propulsion thrusters, from measuring thrust, exhaust velocity and specific impulse to more advanced work like plume characterization, which helps quantify the risk of damage to other parts of the spacecraft. The lab also offers non-invasive testing using laser and optical diagnostics.
“We’ve carved ourselves a niche in electric propulsion as the testing warehouse. All the commercial companies come to us for unbiased testing and measurement,” Spektor said. “We have probably the most comprehensive set of electric propulsion diagnostics that you could find anywhere in the world.”
The recently installed vacuum chamber, with its increased pumping speed, is just the latest addition to this laboratory’s arsenal of testing equipment.
“As electric propulsion devices get larger and more powerful, higher pumping speeds are needed to maintain the proper pressure ratio and allow for accurate testing,” said Spektor. “If there are any potential issues with the thruster, you might not see them at lower pumping speeds because you're not at the conditions you are in space.”
Aerospace is equipped to test the latest large electric propulsion devices or smaller micro-thrusters that go on CubeSats, with tests spanning from just a few hours up to more than a year.
The Future of Electric Propulsion
When operational, the expanded testing facility will allow the lab to double its workload, providing testing services to military and civil customers, as well as a growing field of commercial manufacturers.
One of the first customers will be NASA, testing its 12.5-kilowatt Advanced Electric Propulsion System (AEPS) thruster, which is part of the Gateway mission to orbit the moon.
Other customers are also lining up to access the world-class chamber and benefit from Aerospace’s expertise.
“There are new potential applications developing with our national security space customers for high power electric propulsion,” said Tom Curtiss, director of the Propulsion Science Department. “Watching those come to fruition will be a great thing, and we’ll be able to help reduce the costs of qualifying and developing technology for the next 10 or 20 years.”