The space business is undergoing a disruptive transformation. Capital has been poured into space enterprises, supporting both satellite and launch vehicle production in larger numbers than previously seen. A few companies have constructed manufacturing facilities to produce satellites at faster rates—potentially producing several per day. In comparison with other industries, satellite production could benefit from methodologies employed for mass production of other complex systems (e.g., airplanes, automobiles) that must be reliable. As satellite quantities are scaled up, new methods and approaches will define high-volume production of space systems.
Designing and building satellites have historically been a low-volume endeavor characterized by craft production methods. Each satellite is essentially hand-built and the construction takes years to complete. Keeping manufacturing processes consistent is a challenge when constructing small numbers of hand-built satellites. Even so-called “clone” satellites, although similar, have an exclusive pedigree reflecting workmanship variations, engineering changes from lessons learned, and part changes due to obsolescence.
One historical example of a high-volume, large, satellite constellation was Iridium, for which 98 communications satellites were built in the 1990s and, more recently, 81 satellites for Iridium NEXT. SpaceX, Telesat, and Amazon are planned to have hundreds or even thousands of satellites. Some of these have already started production using new methods. By July 2020 SpaceX’s Starlink placed approximately 600 satellites in orbit.
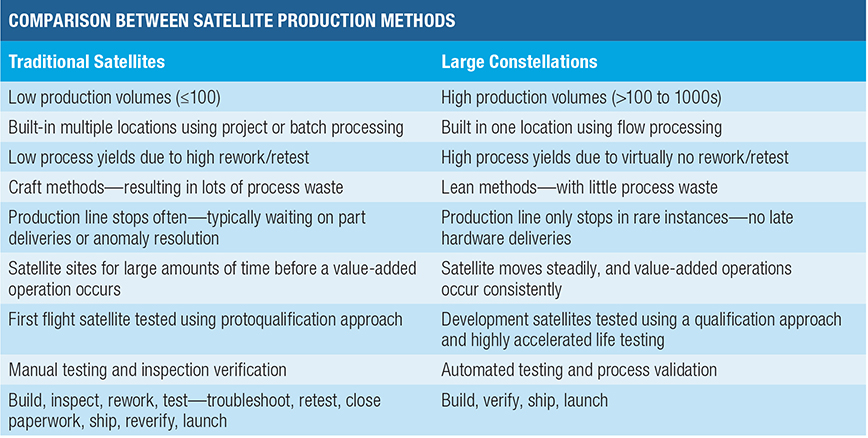
The production scale and capital investment change as production increases from tens to hundreds to thousands of units. Satellites have never been produced in the thousands for a single constellation—different methods and infrastructure for high-volume production (HVP) are required.
HVP is not a new idea. Automobiles have been mass produced since the 1910s and 1920s. Commercial airplanes, automobiles, and consumer electronics all use production approaches that yield insights that can be adapted for use in the manufacture of large constellations of satellites. The table on the first page highlights key differences between traditional satellites versus large constellations.
Design for production (DFP) is an approach that considers the product design, process design, and production planning for a product using a concurrent engineering or “collaborate approach.” DFP basic principles include:
- Ease of manufacturing: Product designs and processes that meet engineering and quality requirements in the easiest way possible—that favor simplicity and standardization
- Efficiency: Processes that minimize time and processing steps through the reduction/elimination of waste using lean production methods
- Economical production: Mature designs and capable processes that allow for high repeatability and value-added processing
Design qualification for objects flown in space has always required rigorous environmental testing to stress the hardware at different test profiles for either qualification, protoqualification, or acceptance levels—which is defined in the environmental testing standard TR-RS-2014-00016. Highly accelerated life testing is an alternate and complementary test strategy that combines environmental and operational stresses to quickly identify failure modes and accelerate testing.
Once a satellite design is qualified, large constellation builders have taken the additional step of flying prototype spacecraft and assessing their on-orbit performance before finalizing their designs and scaling up production. Process verification is applied to the production system (factory, production line, etc.) to ensure it is ready to start high-rate production. In-process controls and measurements provide confidence in product manufacturing consistency.
HVP requires a mission assurance strategy that qualifies the design and the manufacturing process to ensure no learning curve from one unit to the next on the assembly line.
For more information, contact Dave Eccles, Susan Hastings, orJeff Juranek.
Reference
Aerospace Report No. OTR-2020-00640
This story appears in the September 2020 issue of Getting It Right, Collaborating for Mission Success.