In the late 1980s the U.S. automotive industry was facing the “valley of death,” suffering from poor quality products, low productivity, and high costs. Meanwhile Japanese automotive companies were building automobiles of significantly higher quality and reliability, producing them more efficiently with shorter cycle times. With much introspection, U.S. automakers studied the Japanese design and production methods, leading to a transformation of the U.S. auto industry. This begs the question: can the space industry learn anything from the automotive industry?
Here are some of the key automotive lessons learned that can provide valuable insight into high-volume production (HVP) for space systems:
- Engineering and manufacturing not working as an integrated team (i.e., working in silos) results in “over-the-wall engineering” and products that are non-conforming due to variability that is not addressed across organizational departments
- 70% of a product’s cost is in design—invest in design quality and simplification
- Cost is associated with cycle time, and time is money; therefore, efficiency must be addressed
- Building a product using “flow manufacturing and a product layout” is the most efficient method of high-volume production
- Automotive production part approval process enables higher levels of repeatability required to support high production rates
Luckily, there is a set of design and production approaches that addresses these challenges. Robust Design methods and Lean Production methods, when used together, collectively improve the design quality and efficiency of products designed and built. The graphic shown illustrates the collective interface between the two approaches and the specific methods that are used in the automotive industry.
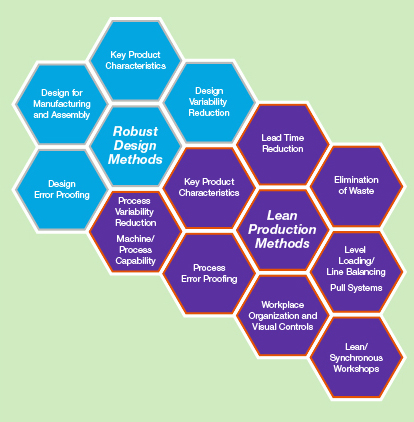
Robust Design methods improve product quality by reducing the sensitivity of product performance due to variations in parts, materials, manufacturing processes, and the operating environment. All these methods are used during the design phase to create a robust product design that has been optimized for cost, simplicity, and producibility.
Lean Production methods eliminate inefficiency throughout manufacturing. Special emphasis is placed on operational efficiency that is caused by waste, unevenness, and overburden in manufacturing processes. A collection of methods (as shown in the figure) is used in manufacturing to address this waste. The basic idea is to develop uniform systems that ensure repeatability and consistency of processes.
Production Part Approval Process is a rigorous standard used in the automotive industry to ensure that all manufacturing processes consistently produce high-quality parts at the required production rates. This is referred to as “run-at-rate production.” There is additional rigor applied to automotive HVP that is not common in the space industry: (1) performing design failure modes and effects analysis to every product level (not just the subsystem level), (2) performing process failure modes and effects analysis on every manufacturing process, and (3) performing measurement systems analysis (a.k.a. gauge repeatability and reproducibility studies) on processes to eliminate sources of measurement error.
As we move into high-volume production of space systems, some of the key focus areas to ensure successful build and delivery are:
- A stricter stance/emphasis on repeatable quality will be required for HVP of space systems
- To achieve high-quality products, sources of excess variation should be understood and controlled
- On-time delivery of parts (that work as intended) is required to support HVP
A two-pronged approach is needed—with opportunities on both the design side and manufacturing side to realize HVP of space systems.
REFERENCE
Aerospace Report No. ATR-2020-01711*
For more information contact Jeff Juranek.
This story appears in the December 2020 issue of Getting It Right, Collaborating for Mission Success.