Smart manufacturing increases production efficiency through the digitization and fusion of manufacturing and design data. It achieves a state of operations in which all relevant information is made available to all stakeholders across the engineering, manufacturing, and supply chain areas—when, where, and how it is needed. The Aerospace Corporation conducted a study to assess the maturity of smart manufacturing and to understand how it will affect the space industry.1
Digital Engineering and Production
Smart manufacturing can be envisioned as the intersection of three domains: digital engineering, the industrial internet, and smart facilities. Digital engineering starts with product design data and uses model-based engineering to drive a digital workflow throughout the product lifecycle. The industrial internet enables monitoring of production through networked equipment and data analytics. Smart facilities apply automation and self-diagnostic sensors and controls to a connected enterprise backbone to increase efficiency.
The integration of these three domains into a proactive cyber-physical system is made possible by the advancement of sensors, processors, and internet technologies that allow information to be analyzed and applied faster and more efficiently on a larger scale than ever before.
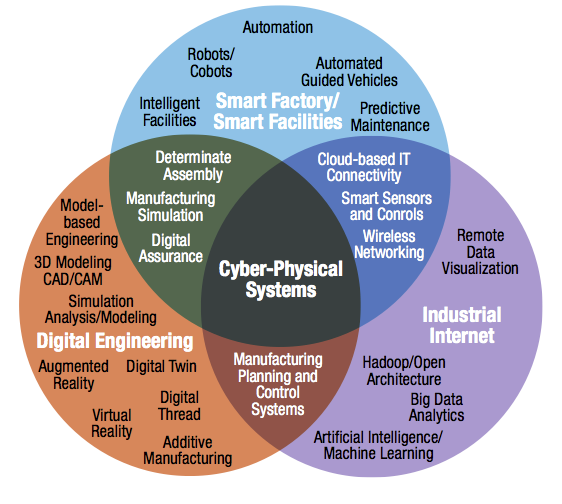
Production Agility
The space industry is transitioning toward new architectures involving constellations of smaller, simpler satellites. To increase production, space contractors will need to move from project-based manufacturing (focused on producing a small number of complex units) to flow manufacturing (focused on producing a high volume of standardized units). Dramatically different workflows based on smart manufacturing will rearrange the value streams and lead to new processes and products. Lean techniques will play an important part in this transition.
Challenges for the space industry include digital engineering with relevant information technology and supplier controls. Space companies have mature design processes but have only just started to digitize the engineering chain. Technical and business processes are being re-engineered to eliminate silos and allow data to flow among different organizations and software tools. Digitization of the engineering process will allow seamless integration across the enterprise.
A Phased Approach
The space industry is gradually phasing in smart manufacturing technologies. As capital equipment is replaced and updated, contractors are installing "smarter" equipment and creating "islands of automation," which achieve greater efficiency for part of the process but do not represent a complete end-to-end solution. Perhaps the greatest benefits of the newer equipment are enhanced process capability and greater precision, which result in higher repeatability.
Technology often disrupts, rendering older methods obsolete. While significant change lies ahead, there is also optimism about the potential for new technologies to increase efficiency and provide widespread benefits across the space industry.
1 Smart Manufacturing and Space Systems, Aerospace Report No. TOR-2018-02099, The Aerospace Corporation, El Segundo, CA (May 14, 2018). Restricted distribution.
This story appeared in the December 2018 issue of Getting It Right, Collaborating for Mission Success.
Subscribe to Getting It Right
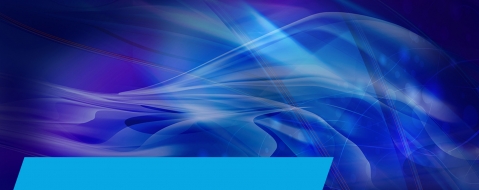