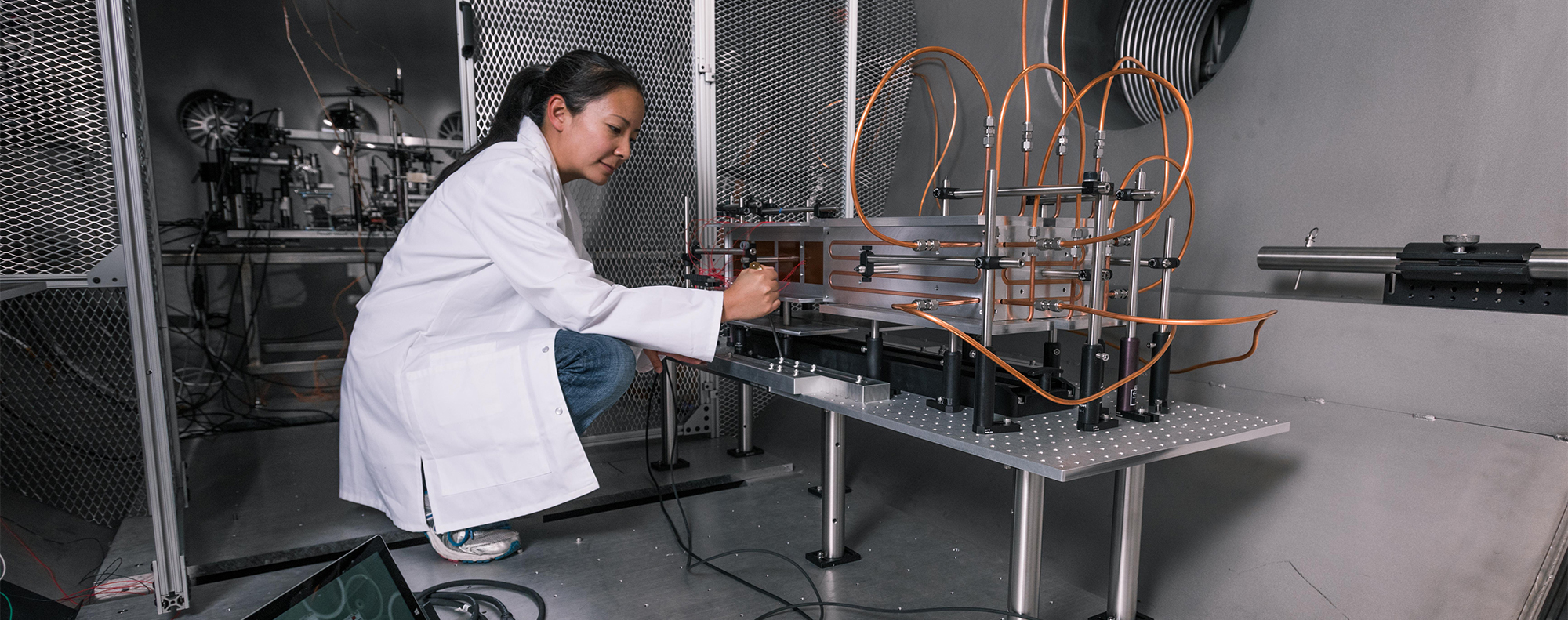
As space technology evolves, one of the major goals in the advancement of space research and exploration will be to reduce the size and costs of launching satellites. The development and deployment of CubeSats and small satellites is an example of realizing this goal.
CubeSats and Small Satellites Propulsion Challenges
Propulsion is important for all satellites. It enables a satellite to maneuver while in orbit, maintain an assigned orbit path and orientation, in addition to a host of other capabilities. Without it, satellites can’t “go” anywhere. Historically, scaling down propulsion devices from large satellites to small satellites has been challenging and largely impractical due to power requirements and sheer size. However, this is changing in today’s space environment. The field of small satellite propulsion is growing, and growing fast — a cursory survey yields over a hundred propulsion device options, fueled largely by the rapid emergence of aerospace start-up companies.
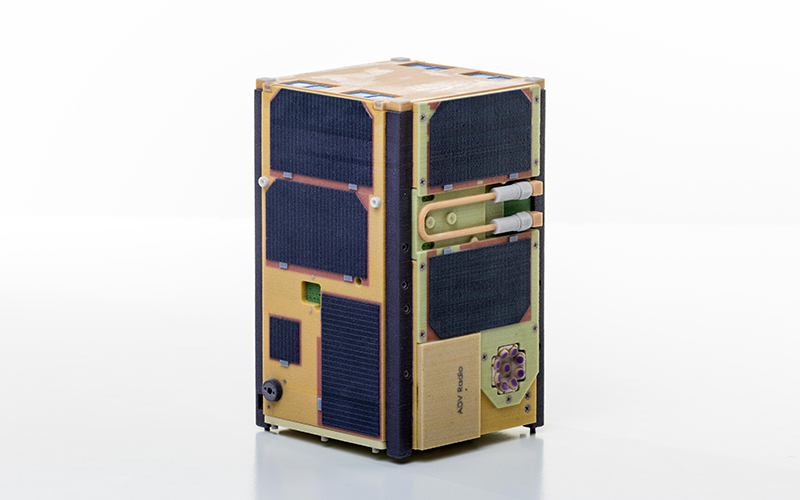
Micropropulsion Testing Facility Services Aerospace Industry
In response to the growth of CubeSats and small satellites, The Aerospace Corporation’s Propulsion Science Department has built a premier micropropulsion testing facility. Nicknamed “The Snake Pit,” the facility possesses extremely precise instruments for testing miniature thrusters. With this facility, Aerospace can perform non-partisan, unbiased testing for small satellite propulsion customers including universities, aerospace start-up companies, and government agencies.
The Snake-Pit testing staff, led by research scientist Dr. Andrea Hsu, test micropropulsion in a vacuum chamber that is used to study how thrusters work in a space-like environment. The chamber uses precise, delicate instruments, designed and built in-house, to measure how much thrust (force) a miniature thruster can produce. Thrust is an important factor in gauging the performance of any propulsion device.
Snake Pit’s Unique Capabilities
Typical amounts of force emitted from micropropulsion thrusters are on the order of hundreds of micronewtons, which is about the force of an eyelash falling on a hand. This may seem tiny, but in space where there is no gravity and no drag to overcome, only very small amounts of force are required for most missions. Testing these tiny amounts of force on Earth, however, poses some unique challenges like vibrational noise suppression, which are addressed in the micropropulsion testing facility.
Other tests include evaluating the performance of the thruster, such as how long it operates and if it experiences any type of failure. The entire testing process takes about a month’s time and the data that is collected is reported to the customer along with any recommendations and feedback.
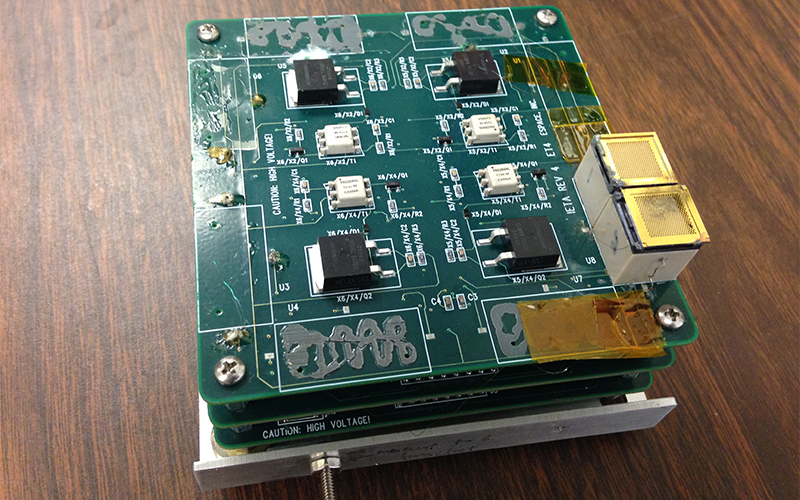
CubeSats Micropropulsion Technology Rises
Aerospace has an ongoing association with the Massachusetts Institute of Technology (MIT) to test its electrospray thrusters, and is also performing testing for commercial companies. “As CubeSats become increasingly capable and access to space becomes more readily available and inexpensive, small satellite propulsion research and development will really be going places,” says Hsu.
All this means the Snake Pit will likely be very busy for the foreseeable future.