Satellites and space vehicles are required to survive extreme environments. Scientists at The Aerospace Corporation specialize in creating and evaluating lubricants that help spacecraft withstand whatever space throws at them.
Every vehicle, from the International Space Station to interstellar probes, runs on many moving parts. Preventing wear and tear on these mechanisms is the job of tribologists, who specialize in the study of interacting surfaces and friction.
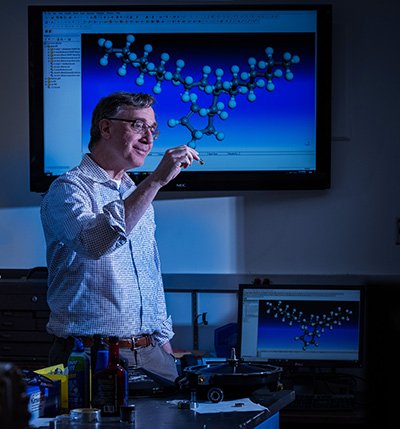
“There are mechanical systems in space operating at thousands of rotations per minute that have to last for 15 years without an oil change,” said Dr. Stephen Didziulis, Director of Aerospace’s Surface Science and Engineering Department.
Choosing the right lubricants requires deep knowledge of not only the compounds themselves, but also an understanding of the surfaces, systems and extreme environment conditions of space involved in a mission.
Liquid lubricants, oils and greases thicken like molasses in extreme cold, become too loose in heat and can evaporate too easily, requiring highly specialized space formulations. Solid lubricants are needed in very cold and contamination-sensitive systems. Examples include Teflon and molybdenum disulfide, a graphite-like substance. Unlike graphite, however, this compound doesn’t require moisture in the air to function, making it ideal for the vacuum of space.
Since vehicles can’t be repaired after they leave the Earth, operators must be certain that their systems will function for the full duration of their missions. Aerospace houses the world’s foremost capabilities for the testing and verification of space lubricants, serving as a crucial resource for the industry’s toughest tribological challenges.
Tribology in Action
In July, NASA’s Jet Propulsion Laboratory tasked Aerospace with a critical lubrication evaluation for the Perseverance rover, a part of the Mars 2020 mission. Perseverance, set to land on the Red Planet in February 2021, will look for signs of ancient life by collecting rock and soil samples for possible return to Earth in future missions.
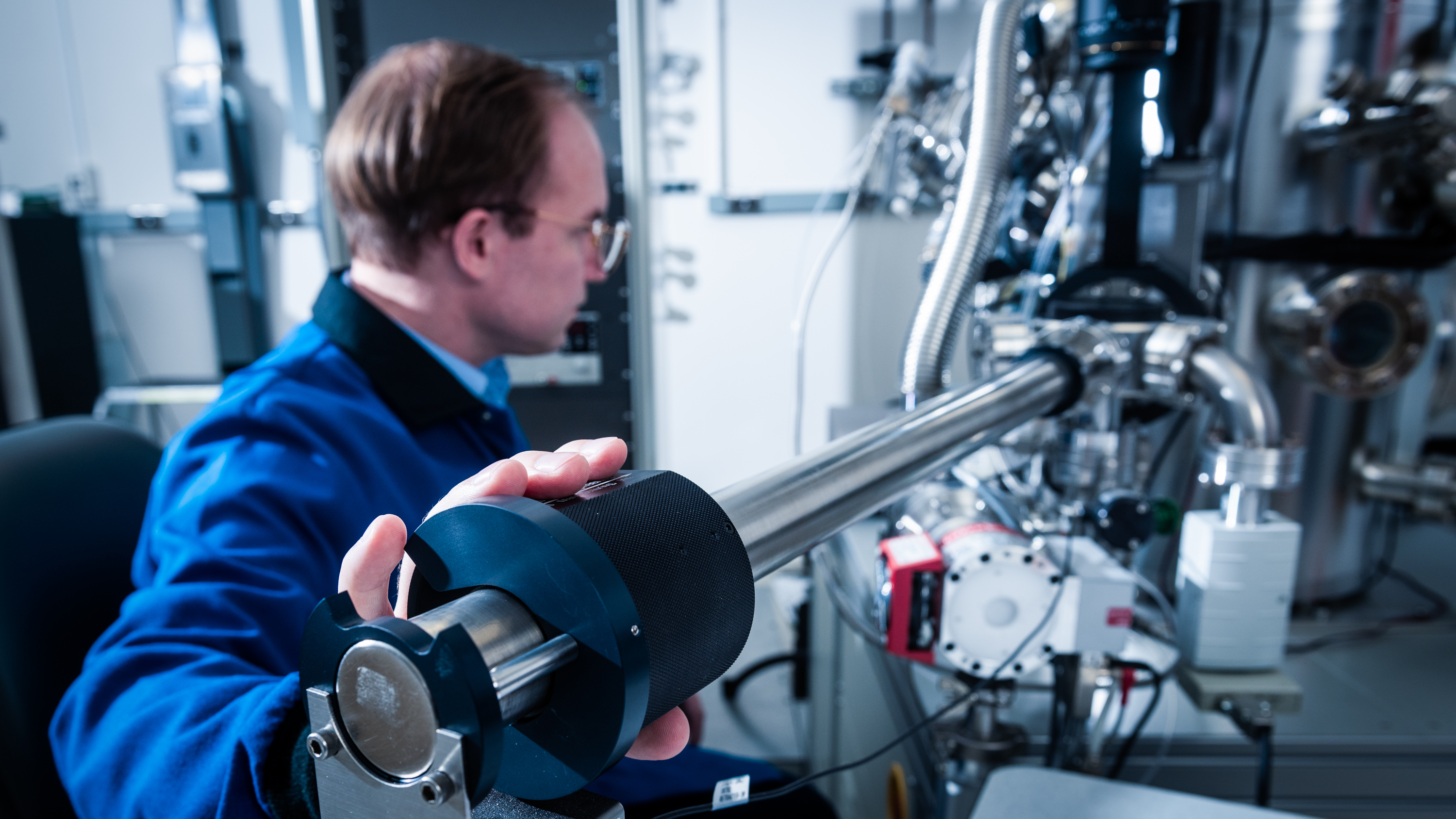
To prevent the contamination of the samples, the rover’s equipment must be sterilized. However, this process had an unexpected effect on the solid lubricants needed to manipulate, seal and deposit the collection tubes on the Martian surface.
JPL engaged with the Aerospace tribology team to obtain a better understanding of the impact of sterilization on the lubricant and to define a less damaging procedure to ensure that the lubricants would adequately function.
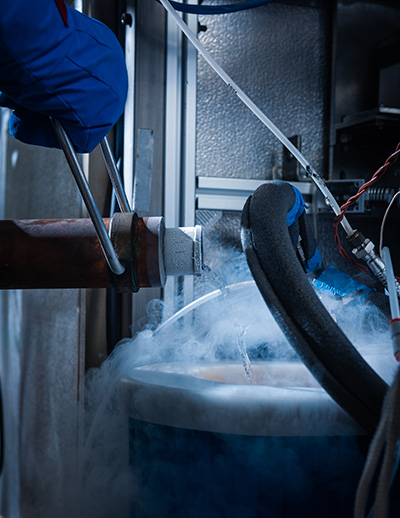
“They wanted to kill off any microbes in the equipment,” Didziulis said. “But the team was concerned that the sanitization could destroy the lubricants.”
The Aerospace team proceeded to test and analyze lubricants subjected to a less damaging sterilization process and prove that they would work in the Martian environment.
Fortunately, Aerospace’s lab contains one of the few instruments in existence capable of testing a lubricant under Mars conditions: carbon dioxide-heavy air, blistering cold and low pressure.
Using a unique rotating stage cooled with liquid nitrogen in a vacuum chamber, the team proved that the Martian atmosphere would not harm the performance of the solid lubricants, enabling the rover to launch on schedule at the end of July.
The team’s unique capabilities, combined with the corporation’s breadth of space systems experience, make Aerospace a sought-after authority on lubrication issues.
“Most people don't care about the space environment when they do tribology. Most tribologists reside in fields like aviation, automotive or biomechanical engineering,” Didziulis said. “But it’s an essential area for space, so we stay very busy.”