The Mission Assurance Improvement Workshop (MAIW), a national space program dedicated to the development of mission success best practices, organized a team made up of engineers from leading aerospace companies including The Aerospace Corporation, to investigate the causes of CubeSat mission failure and create recommendations on how to improve mission success. Their findings were documented in a paper, "Improving Mission Success of CubeSats."

CubeSats Are Popular But Frequently Fail
Once the domain of universities which built CubeSats as a learning tool, in recent years, the wide use of CubeSats have boomed at an astonishing rate. Commercial companies, researchers, academia and the government are all building CubeSats for various operational missions. Commercial companies use these small satellites for global imaging and communications while researchers and academia continue to use CubeSats for research and development. A growing CubeSat customer is the government who is looking to use them for numerous applications such as technical demonstrations, scientific experiments, imaging, communications, and climate monitoring.
Despite the proliferation of CubeSats, one fact tends to get overlooked: CubeSats have high failure rates due to their low costs and their fast development cycle. Studies show academia success rates average only 45 percent while commercial companies have an average success rate of around 77 percent. Missions were considered successful if the CubeSat operated on orbit for 60 days or longer.
Reasons Cubesats Have High Mission Failure Rates
The MAIW CubeSat team was also tasked with evaluating the prospects for improving the mission success rate. The group surveyed a number of academic, commercial, and government organizations engaged in the design and development of CubeSats to identify their most common problem areas. These areas included the communication system, the ground segment, and power systems.
Launch is also a significant cause of design and development problems. Since primary payloads do not wait for secondary payloads, CubeSat developers often have to compress their testing programs to meet inflexible launch dates. Conversely, some CubeSats must wait a long time for a launch opportunity, which increases the chance of the satellite degrading as it sits.
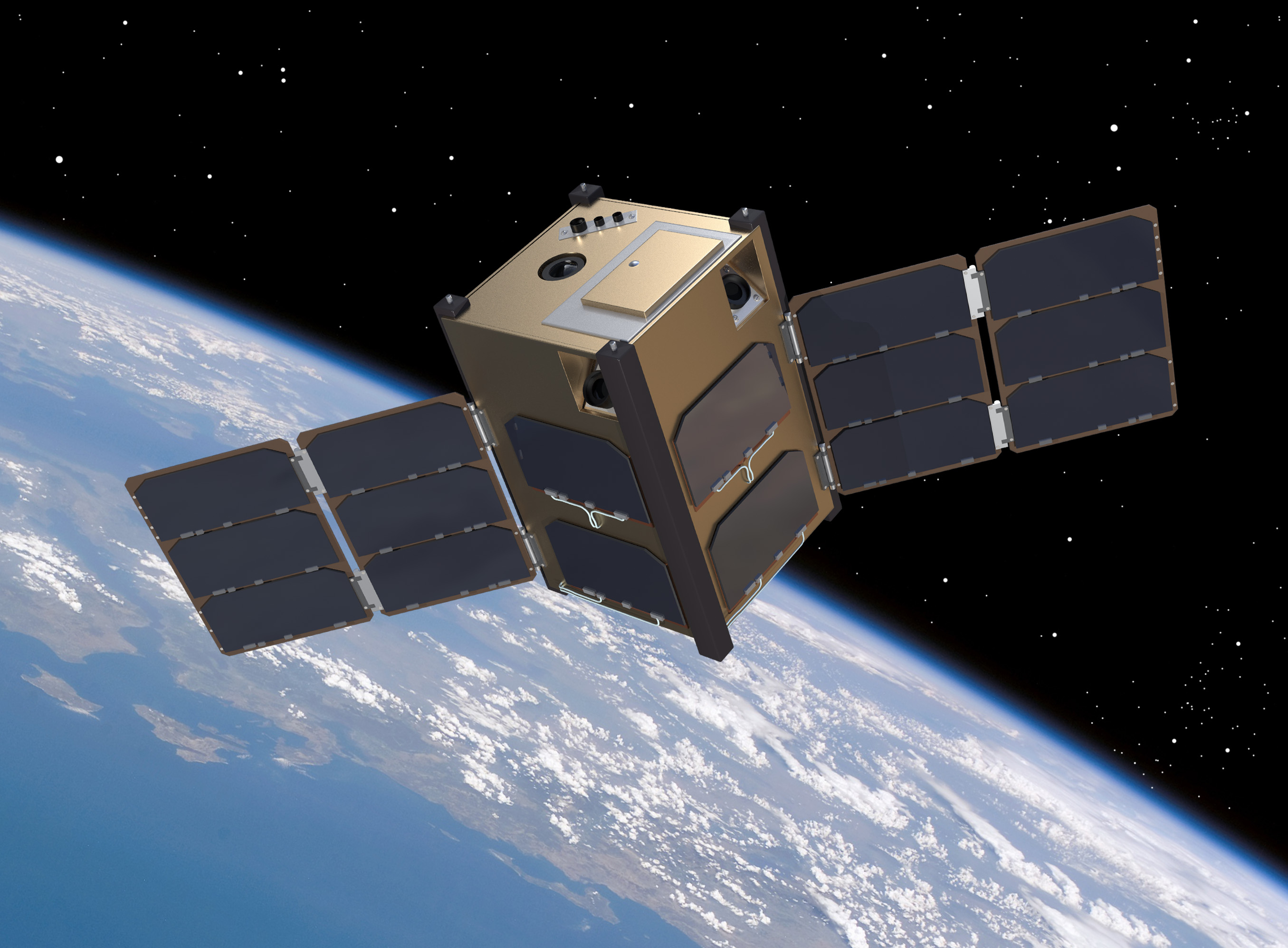
Mission Success Guidelines For CubeSat Developers
Based on their research, the team compiled a set of eight recommendations for CubeSat developers to improve their chances for mission success.:
- Define the scope, goals, and success criteria at the start. Every organization will have a different definition of mission success and even a failure on orbit can be seen as valuable data or a learning experience.
- Allot sufficient time for integration, verification, and testing— preferably, one-third to one-half of the overall schedule. Testing, testing and more testing, is key to CubeSat success. Ideally, the full battery of tests would include thermal vacuum, RF compatibility, deployment, hardware-in-the-loop, and software testing.
- Conduct risk-based mission assurance, with an initial risk assessment to help prioritize tests and reviews. Focus on thinking through the problems that “keep you up at night,” those issues that are most critical to your mission success. Identifying these issues early on will help in planning on how to mitigate these risks.
- Design for simplicity and robustness. Don’t over-engineer and add unnecessary complexity to the CubeSat design. Simpler designs that can be easily reworked will pose fewer problems.
- Include experienced personnel on the team. Teams with experienced designers and mentors typically achieved greater success.
- Stock spare components to enable parallel development and more rigorous testing. Most CubeSats are assembled from standardized parts that are not fully protected against the space environment so designers should plan accordingly.
- Perform at least four mission assurance tests—day-in-the-life testing, communication link testing, power system testing, and thermal testing. Regular reviews, both formal and informal, help to boost success rates.
- View subsystem datasheets with skepticism. CubeSats are built with commercial parts that are sold with datasheets with information about how the part performed under ideal conditions. Space is not an ideal condition for testing, so always test the parts in an environment similar to where the CubeSat will be deployed.
Most of these broad guidelines can be tailored and implemented without much cost. Although they seem to be common sense, the study team found that few CubeSat developers followed all these recommendations. The team hopes that in the future, they can collect data from developers who actually followed all these guidelines to measure any increases in CubeSat mission success.
This article originally appeared in the March 2018 issue of "Getting It Right."