Additive manufacturing (also known as AM, or 3D printing) presents tantalizing possibilities for use in space. Engineers hope to one day use the process to print parts, tools and other materials that the aerospace industry has historically relied upon machining and molding to manufacture.
These traditional manufacturing methods require material to be carved or shaped until it resembles the desired product such as a bolt or nut, which can make the creation of certain items difficult or even impossible. In contrast, 3D printing allows parts to be manufactured by adding material in minuscule layers that build up to create a desired shape. This process involves the use of a computer and CAD software, which enable a specialized printer to “print” a specific shape or part.
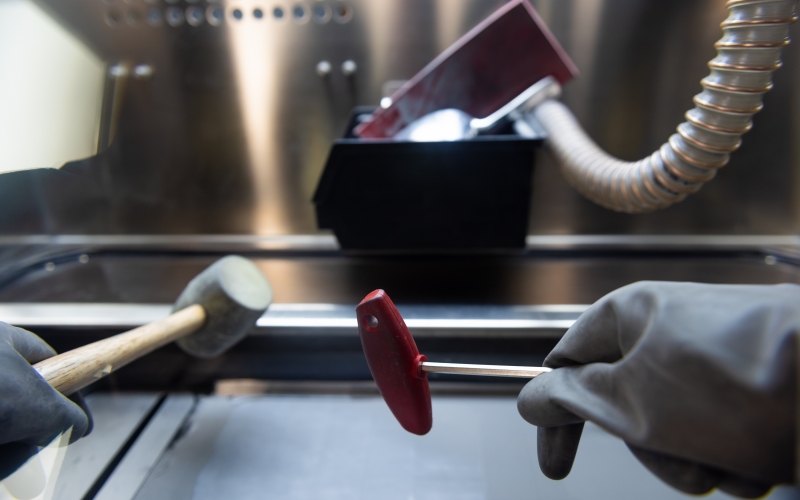
The durability of these parts depends on the type of material used to print them. An ever-increasing range of plastics, polymers, ceramics, and metals are now available. The Aerospace Corporation is currently targeting two classes of material for use in space: Inconel and Ultem. Aerospace researchers are exploring the microstructures of these materials in an effort to engineer new materials that are optimized for space applications, which require increased resilience and resistance to extreme temperatures.
The Inconel family of nickel alloys is currently used in a wide range of industries and applications around the world. Aerospace scientists have recently focused their attention on Inconel 718, a heat-treatable nickel-chromium-iron alloy designed to resist a wide range of severely corrosive environments while retaining its high yield and tensile properties at high temperatures and pressure. Now widely used in space flight systems due to its weldability and cryogenic properties, Inconel 718 retains its strength over a wide temperature range. It pulls this off by forming a thick, stable oxide layer when heated, which protects its surface during high-temperature applications where aluminum and steel would deform and fail.
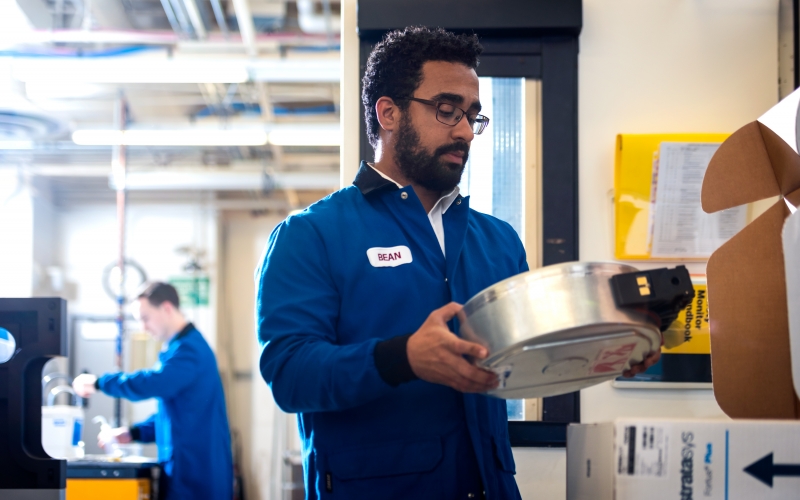
Ultem is another promising material. As part of a family of amorphous thermoplastic polyetherimide (PEI) resins, Ultem can withstand extreme temperatures while offering high strength and stiffness properties in addition to broad chemical resistance. Ultem 9085 has exhibited immense potential due to its superior mechanical performance and strength-to-weight ratio. Ultem 9085’s strength, light weight, and flame-retardant qualities make it an ideal candidate for aerospace and automotive applications. Aerospace researchers are now exploring the suitability of Ultem 9085 for production-grade components and testing its potential for creating prototypes and production tools.
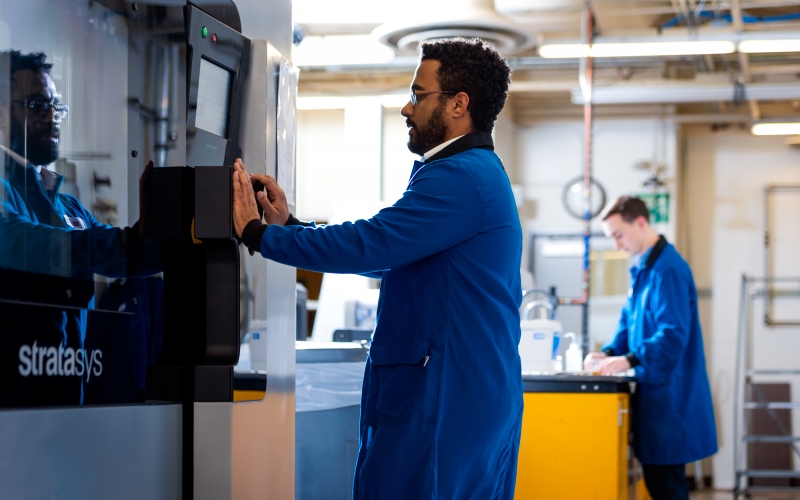
Aerospace researchers are also working to uncover as-of-yet unknown qualities of these materials and their microstructures in hopes of revealing any potential failures that could jeopardize their use in space and other endeavors. The hope is that these research efforts will yield materials that can withstand the rigors of space and lead to the development of manufacturing techniques that provide rapid production of parts that are challenging or otherwise impossible to create. Once proven and deployed, engineers will to be able to print parts, tools and even entire habitats on the ground or on the fly.