Test and analysis can assess electronics reliability, but budget and time constrained programs often shun analysis as too expensive or challenging. In many cases, little to no analysis is performed. But is testing alone more cost effective in improving reliability?
Test tells us what is. Test has many potential pitfalls: bad data, bad equipment, and bad interpretation. Test determines typical performance and requires parts to be produced prior to build. Test alone can miss specified requirements for beginning or end-of-life, overlook derived requirements,f and is only valid for the measurement lot.
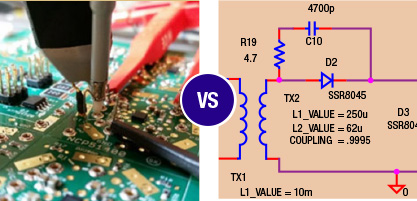
Analysis tells us what it could be. Analysis computes margins, risk, parameter sensitivity, and identifies fatal and rare events. Performance aspects are examined, quantified, and evaluated through a series of analyses (worst-case circuit analysis, stress and derating, failure mode, effects and criticality analysis, and mean time between failures).
Analysis should target tolerance ratios, heritage reference designs, and stress levels combined with failure modes analysis. Analysis problem discovery is in the derived requirements, minor design changes, signal integrity-power integrity, and at the interfaces/connectors.
Checklists exist with guidelines for selected applications based on historical use and current needs.1 Analysis can gain confidence from nominal performance and limited statistical test data. Test and analysis make for a powerful combination if applied complementarily even when constrained.
Go to aeng.com for more information, or contact Charles Hymowitz, 310.216.1144, charles@aeng.com
1TOR-2012(8960)-4 REV A—Electrical Design Worst-Case Circuit Analysis Guidelines and Draft Standard
Photo courtesy of Picotest.com and AEi Systems, LLC
This story appears in the March 2020 issue of Getting It Right, Collaborating for Mission Success.
Subscribe to Getting It Right
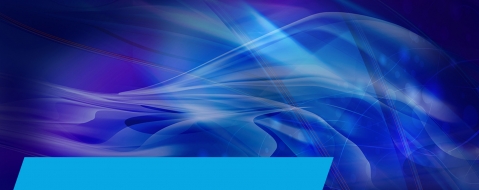