Historically, semiconductor manufacturers have used gold wire to connect the semiconductor die to the lead frames and external pins. However, rising gold prices are driving manufacturers toward less-expensive alternative materials such as copper for use in high-volume commercial plastic package devices.
Military standards such as MIL-STD-883 do not define requirements for copper bond wires, and therefore manufacturers are using qualification and process monitoring developed for gold wire to qualify the copper bond wire technology. Although copper bond wire designs are moving forward for commercial applications, there are concerns with quality and reliability when using copper bond wires in high-reliability military electronics with a long mission life.
Potential failure modes of copper bond wires include corrosion, intermetallic growth, oxidation, susceptibility to cleaning process chemicals, and changes in electrical performance. Limited reliability data is available in plastic encapsulated microcircuits (PEMs). Some field failure reports have indicated failures associated with ball bond and crescent bond fractures.
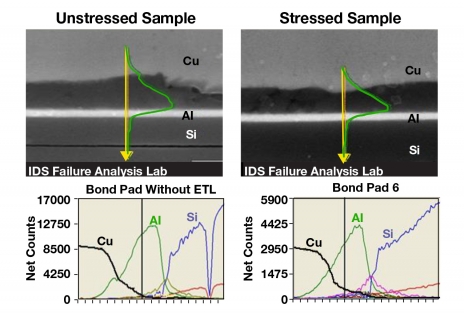
Per J-STD-020, copper PEMs were subjected to bake-out, humidity testing, temperature cycling, and surface mount technology reflow. Cross-sectioned samples of environmentally stressed PEMs were compared to cross-sectioned samples of unstressed PEMs in a scanning electron microscope (SEM), and the effect of the environmental stress was found to be negligible.
The diffusion between the copper bond wire and aluminum bond pad results in an intermetallic phase between the two materials. In both the stressed and unstressed samples, aluminum layers were identified that exhibited signs of cracking and voiding.
Several component manufacturers are transitioning from gold bond wires to copper bond wires without reflecting changes in part numbers or without communicating these changes with a part change notification.
Since there is currently no official qualification procedure for the use of copper bond wires, an update to military specifications should be considered and should include increased stress levels during qualification, extended life testing to determine long-term reliability, and wire pull and ball shear specifications for copper bond wires.
This story appears in the March 2019 issue of Getting It Right, Collaborating for Mission Success.
Subscribe to Getting It Right
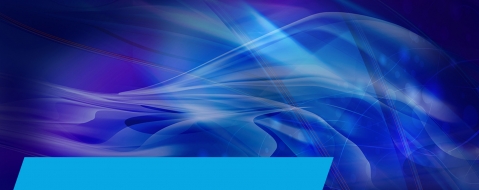