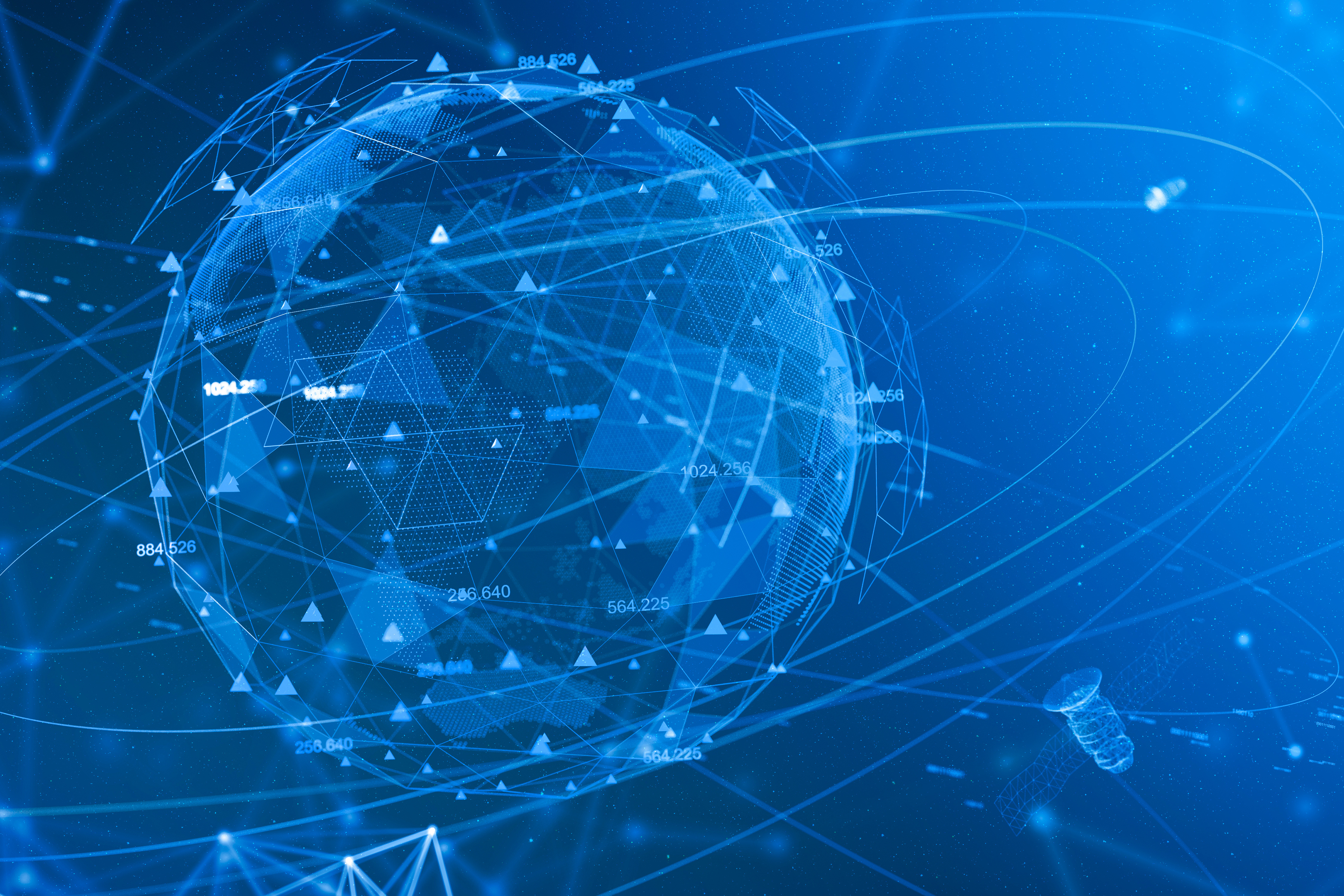
Continued advancements in 3D printing have accelerated its transition from a once niche technology to what is now an essential application in modern engineering. The technology is increasingly being used in a variety of industries to create ever more complex objects and is now making inroads into fields in which traditional manufacturing methods have been the norm.
Just a few years ago, the use of 3D-printed satellite components was largely experimental, with relatively few parts being flown in space missions and payloads. Today, nearly all new satellites have at least some 3D-printed components, and satellite manufacturers have embraced 3D printing technology as a means of reducing cost and accelerating production for increasingly capable spacecraft.
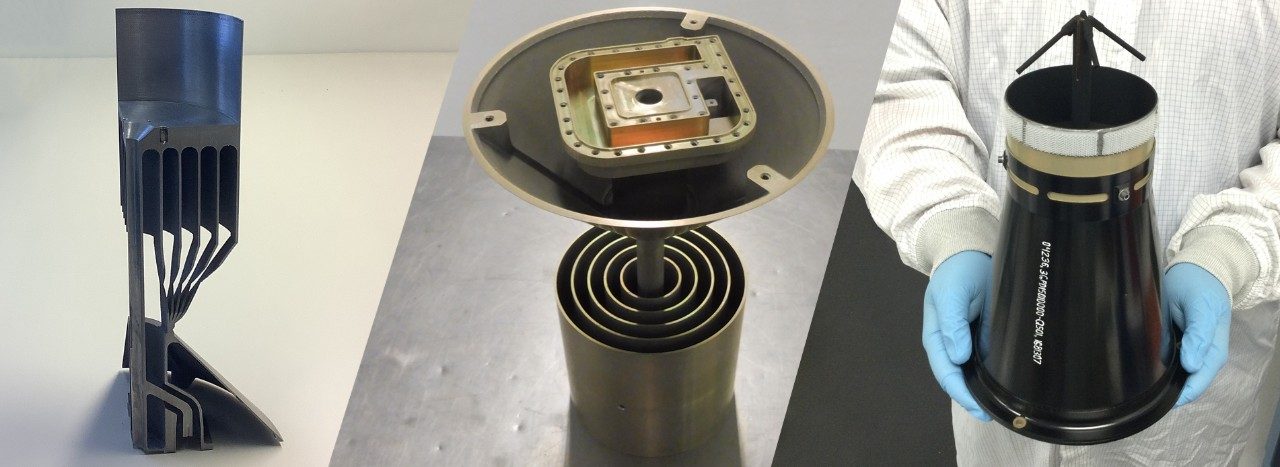
While most 3D-printed parts are relatively simple components designed to ensure the integrity of a spacecraft’s build, The Aerospace Corporation recently contributed to the qualification of a 3D-printed omnidirectional antenna assembly for telemetry, tracking and command for use on two satellites for the Global Positioning System (GPS), making it the first 3D-printed GPS configuration item to be space-qualified.
“There’s a tremendous advantage to producing components using 3D printing,” said Benjamin J. Likar, Senior Project Engineer for GPS Satellite Systems. “3D printing can now produce complex parts, without the need for traditional soldering and welding and the structural issues they can factor in. Once you understand the characteristics of the material, you can design for it, make sure it’s suitable and can fulfill your structural analysis requirements.”