Have you ever wondered how deep space missions are able to send images from the edge of the solar system back to Earth? These long-distance transmissions are made possible by a highly specialized type of vacuum tube. While the earliest vacuum tubes date back to 1904, by mid-century they had evolved to become ubiquitous in households worldwide. In the latter part of World War II, a high power vacuum tube that operates at microwave frequencies was invented. It’s known as a travelling wave tube (TWT), and it continues to play a vital role in space communication to this day.
The modern TWTs used today are sophisticated vacuum electronic devices made of advanced metal alloys and ceramics, and bear little resemblance to their lower frequency, glass-enveloped predecessors. For higher-powered needs, such as for satellite transponders, a TWT amplifier (TWTA) is used to provide critical communication functions by converting weak input signals into high-powered ones. TWTAs are a combination of a traveling wave tube and an electronic power conditioner that converts the spacecraft bus voltage to the necessary higher voltage levels, with added command and telemetry functions. TWTAs amplify RF signals by absorbing power from a beam of electrons as it passes down the tube.
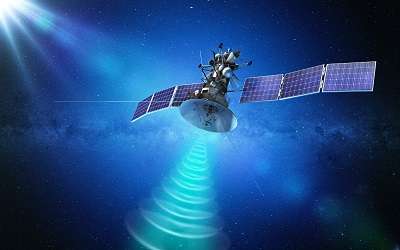
“Before being superseded by transistors, vacuum tubes were essential components of consumer-grade television sets and radios up until the 1970s. People are often surprised to learn that TWT amplifiers weigh less and perform more efficiently than their transistor counterparts,” said Michael Muha, Senior Engineering Specialist at Aerospace.
When proper design practices and qualified manufacturing processes are followed, the TWT is unsurpassed in providing robust and reliable service in critical space applications. However, their performance comes at a considerable price.
The Aerospace Corporation recently helped identify and resolve a technical challenge involving a customer’s TWT, while also providing an innovative approach to remediation which allowed the customer’s project to proceed without significant delays or cost overruns. Individual units can cost as much as $1,000,000 to produce and can require more than a year to build or qualify using current protocols. TWTs are structurally complex and therefore reliant upon high manufacturing standards which, if not attained, can lead to potentially catastrophic design flaws and system failures. Aerospace’s ingenious solution may well establish better, faster and more cost-effective practices going forward.
TWTs: Reliable, but Not Infallible
Aerospace engineers were recently tasked with providing a comprehensive assessment of a high-voltage connection failure on a TWTA, which occurred during a final thermal vacuum test, resulting in electricity “jumping” to a nearby grounded object (a phenomenon known as electrical arcing). While TWT high-voltage connections are typically encapsulated with a polymer material to prevent this from occurring, an accidental void in the polymer led to an electrical arcing incident, which rendered the TWT inoperative.
The assessment by the engineers included an optimal rework scenario complicated by the risk of damage to the TWT during rework. TWTs are typically mounted permanently to a base plate that is not designed to be taken apart once assembled. As per Samuel S. Osofsky, Director of Aerospace’s Communications Electronics Department, “If you have to take (a TWT) off its base plate it breaks up the configuration, and every configuration that you break, you have to re-test.” The inherent risk was not limited to a broken flight interface, but total loss of the TWT itself. Manufacturing of a new unit could take up to 60 weeks.
Hence, the race was on to find a means of repairing the TWT without separating it from its base plate. The deceptively simple solution bore all the hallmarks of Aerospace ingenuity, involving the creation of a new encapsulation mold that could be placed on the damaged TWT in situ, with the help of additive manufacturing, more commonly known as 3D printing.
Additive Manufacturing to the Rescue
While most 3D printers can produce components using various types of plastic, these print mediums lacked sufficient resolution and design fidelity needed for the rework. Fortunately, several 3D printing options were available at Aerospace, which allowed for resin-based or metal alloy print mediums. Upon identifying a potential solution to the problem, Muha was able to reach across the enterprise and collaborate with other Aerospace experts to bring the idea to fruition.
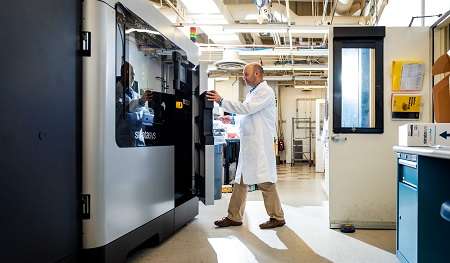
“Aerospace has a lot of resources because we study manufacturing techniques and we look at different ways of manufacturing parts for space applications, so we have a lot of resources in that area, in addition to the diagnostic capabilities and a lot of multidisciplinary expertise leveraged in this investigation,” said Muha.
Muha, an esteemed expert in traveling wave tube technology with 30 years of experience in the field, enlisted the help of fellow Aerospace engineers Oliver Ambrosia in Digital Communication Implementation, and Tait D. McLouth and David Witkin in the Materials Science Department.
As per McLouth, Advanced Degree Fellow at Aerospace, the proposed mold was a two-piece clamshell design that fit in the confined space between the high voltage connection to be encapsulated and the base plate, and conformed exactly to the required TWT’s encapsulated high voltage feedthrough geometry. “It looked like a stepped cylinder with two openings; one to inject the resin and another to allow the excess encapsulant to come out. And it took about four hours to print,” McLouth said. While a similar remediation had been attempted by the customer, their 3D printer could only yield a rough exterior surface to their mold, imparting a similarly rough texture to the encapsulating resin which precluded transparency. This also rendered flight qualification inspection impossible.
“You couldn’t see into it clearly to identify the presence or absence of voids, or other defects,” Muha said. After some initial Aerospace-printed polymer molds proved unsatisfactory, the decision was made to design and print a mold using nickel-based superalloy Inconel 718, which provided the required smooth texture and transparency to the feedthrough encapsulation. This approach proved to be a resounding success, ensuring the ability to rule out defects in the injected polymer while also proving the feasibility of disassembly-free TWT repairs.
Creating Agility and Resiliency for Space
This new approach to remediation has far-reaching implications. Until now, a failure of this type would customarily have required a far higher risk rework of the TWT, possibly resulting in schedule delays and exponential cost increases across several programs and satellites. The long-term implications were equally troubling. As per Muha, “These kinds of defects, if they were undetected, could have resulted in a total loss of the mission because the TWT protection circuits will not allow the TWT to be turned on again.”
While most spacecraft fly so-called “redundant” systems that are intended to serve as backups to primary systems, these redundant systems are not typically activated until much later in the mission (in most cases, years). The failure of this particular TWT could have caused a drastic reduction in the mission’s total life expectancy.
“Believe it or not, after a comprehensive rework, everything was still delivered within the original period of performance for the contract, and under-budget as well, even accounting for the rework of all those units,” Muha adds. “We were under-budget and well ahead of schedule for the entire delivery, for the entire flight set.”
In demonstrating the viability of this new reworking methodology, the Aerospace Corporation has once again leveraged its renowned technical expertise and problem-solving to provide an expedited and cost-effective solution to a seemingly intractable challenge. As per Witkin, Senior Scientist at Aerospace, “Aerospace has proven that you can enable production with a quick turnaround, without having to rely upon traditional supply chains and the delays they entail.”