The ongoing space debris problem poses a significant threat for the future of the rapidly growing space industry. The need for innovative solutions to address this challenge has led experts to seek new methods and develop novel technologies that can mitigate further congestion in Low Earth Orbit (LEO). The Aerospace Corporation continues to be at the forefront in advancing concepts, strategies and capabilities that will ensure sustainable access to space for the future.
Recently, a team at Aerospace developed a prototype deorbit motor that could enable space operators to safely retire their spacecraft on demand. This is now more essential than ever to space missions given the recent requirements adopted by the Federal Communications Commission (FCC). The new rule requires space operators in LEO to deorbit their satellites within five years—instead of 25 years—of the completion of their mission, making end-of-mission capabilities critical to the space architectures of the future.
“The world is growing more and more dependent on the use of space, however, that use is becoming more stressed and challenged,” said Jerry Fuller, Senior Engineering Specialist at Aerospace. “The risk of a debris collision is greater now than it's ever been. And at the same time, there are plans to put many more satellites and many more constellations into space. We need to start developing capabilities that will allow space operators to successfully complete their missions without exacerbating the problem.”
Fuller added that Aerospace’s depth of technical expertise and innovation can be leveraged as a more active resource for the global space community in reducing the debris problem.
“Aerospace’s technology leadership should allow it to play a greater role in debris mitigation,” he said. “This rocket motor technology is one of several components that Aerospace has developed toward that end.”
Meeting the Need for Deorbiting Capabilities
The deorbit motor is designed to be integrated into a spacecraft —such as a CubeSat— using a commercial off-the-shelf (COTS) solid-propellant rocket. What makes it unique is a connected deflector plate and nozzle that creates spin-stabilized axial thrust to enable controlled reentry. As the motor comes up to pressure, the deflector plate acts as an ablative surface and forces gases through various vanes circling the plate, causing the entire satellite to rotate. Once the ablative surface burns away, the motor exhaust exits in the typical fashion, producing the desired deorbit impulse.
“The deorbit motor combines the functions of a spin motor and a thrust motor into a single unit, improving Size, Weight and Power (SWaP) as well as reliability,” Fuller said. “Satellite programs that don’t have the overhead needed for traditional Thrust Vector Control (TVC) can successfully deorbit if they can be oriented in the ram direction (aligned with the direction of flight). In fact, satellites that have lost reaction wheel control might still deorbit, if they still have attitude knowledge and can tumble into the right orientation.”
Most small satellite will have to operate in the lower portions of LEO (about 600 kilometers or below) to rely on drag for deorbit. Above that, there is not enough atmosphere to have much of an effect within five years.
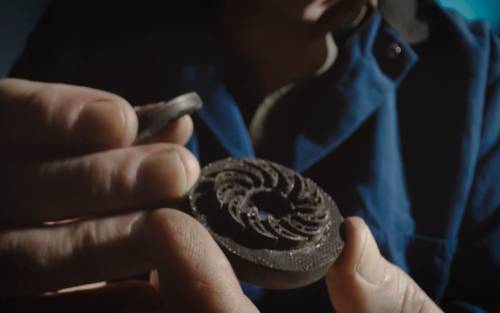
In the past, natural deorbit was less of a concern when the time allowance was up to 25 years. But now with the shorter deorbit allowance, satellites that can’t deorbit naturally by drag will require enhancing elements like tethers, chutes and balloons to meet the new regulations. More sophisticated satellites can use electric propulsion to lower their orbit, but this is still a slow process. The Deorbit Motor, can exit from a much higher altitude than could be done by drag alone and can do it quickly, allowing fewer opportunities for a catastrophic interaction with debris or another satellite
Given the FCC’s new requirements, the deorbit motor could enable space operators to incorporate necessary capabilities to retire their space assets more responsibly once a mission has been completed, while raising the operating altitude well above that where drag could be relied upon.
“The space community is undergoing significant changes in the number and nature of operational satellites and in the diversity of operators and missions,” said Marlon Sorge, Technical Fellow at Aerospace and policy expert for the Center for Orbital and Reentry Debris Studies (CORDS). “These changes are putting a strain on the existing debris mitigation practices. Aerospace is providing our government customers with a quantitative understanding of the new challenges along with possible solutions.”
Creating Solutions Through Collaboration Across Disciplines
Aerospace’s contributions to shaping the understanding of space debris and space traffic management has been quite considerable, starting from the early days of the space era. What may be less known is that Aerospace has also developed and flown experiments, advancing technologies that can be useful in debris mitigation and debris removal.
In the process of developing the deorbit motor, the cross-discipline team of experts at Aerospace collaborated to explore the possibilities of creating a motor that could lower the orbit of any sized satellite, especially smaller ones with less sophistication.
Several different approaches were initially considered, including an arrangement of tractor motors. One approach attempted using a single tractor motor with multiple nozzles changing the shape during the burn to produce spin, followed by thrust. Fuller, along with Senior Project Leader Jeff Lang, collaborated with a breadth of experts across Aerospace, including propulsion, modeling and simulation and control analysis to execute numerous static test experiments and modeling and simulation work. Together, they were able to bring the concept to fruition.
“I come up with these crazy ideas and Jeff is just amazing at making them real,” Fuller said.

The breakthrough happened when they arrived at testing the axial motor approach. The team was able to conduct a successful static test, followed by a successful flight test that demonstrated the intended end result: the deorbit motor.
“In a complicated system, it is difficult to get everything to go exactly as planned.” said Lang. “In our final flight test, using off the shelf, hobby grade components, everything in our test worked just as planned. It was an exciting way to finish off the project.”
Advancing the Bigger Picture
New innovations like the deorbit motor play a vital part in the broader effort to address the concerns of an increasingly congested space environment. Aerospace’s depth of expertise supports a wide breadth of collaborative activities across diverse space stakeholders—from policy, strategy to technical—enabling the development of new and novel approaches to combat the space debris problem.
Capabilities like the deorbit motor—and more importantly, the spirit of ingenuity of the people developing them—bring forth much-needed solutions that can advance agility and flexibility to how missions are planned and executed. Future missions will need to implement new capabilities and concepts to improve the sustainability of space architectures and the broader space ecosystem.
“Aerospace has a long history in the analysis and theoretical understanding of space debris and management,” said Fuller. “This innovation can contribute more directly to deorbiting small satellites, very quickly after their missions are completed.”