Continued advancements in 3D printing have accelerated its transition from a once niche technology to what is now an essential application in modern engineering. The technology is increasingly being used in a variety of industries to create ever more complex objects and is now making inroads into fields in which traditional manufacturing methods have been the norm.
Just a few years ago, the use of 3D-printed satellite components was largely experimental, with relatively few parts being flown in space missions and payloads. Today, nearly all new satellites have at least some 3D-printed components, and satellite manufacturers have embraced 3D printing technology as a means of reducing cost and accelerating production for increasingly capable spacecraft.
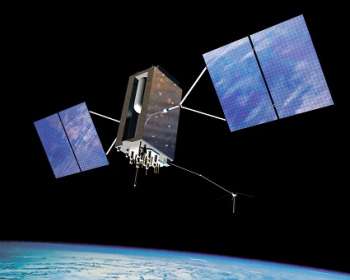
While most 3D-printed parts are relatively simple components designed to ensure the integrity of a spacecraft’s build, The Aerospace Corporation recently contributed to the qualification of a 3D-printed omnidirectional antenna assembly for telemetry, tracking and command for use on two satellites for the Global Positioning System (GPS), making it the first 3D-printed GPS configuration item to be space-qualified.
“There’s a tremendous advantage to producing components using 3D printing,” said Benjamin J. Likar, Senior Project Engineer for GPS Satellite Systems. “3D printing can now produce complex parts, without the need for traditional soldering and welding and the structural issues they can factor in. Once you understand the characteristics of the material, you can design for it, make sure it’s suitable and can fulfill your structural analysis requirements.”
This milestone was the culmination of roughly three years of close collaboration between Aerospace and the contractor in support of the government customer, a process that required consensus on the qualification of the printing material and successful critical design review, qualification and acceptance testing of the antennas themselves. Also noteworthy is the fact that there were no industry standards for qualification of 3D-printed satellite hardware prior to Aerospace’s involvement in this effort.
“To be space-qualified, an item needs to be tested and analyzed, taking into consideration every situation or condition it could encounter,” said Alfred K. Jung, Senior Project Engineer for GPS Space Systems Engineering and Integration at Aerospace. “It’s an ‘above and beyond’ approach to testing and analysis, in which you confirm that not just the design is good, but the manufacturing processes are good and the suppliers are good. This way, everything is taken into account, and you can have full confidence in the hardware.”
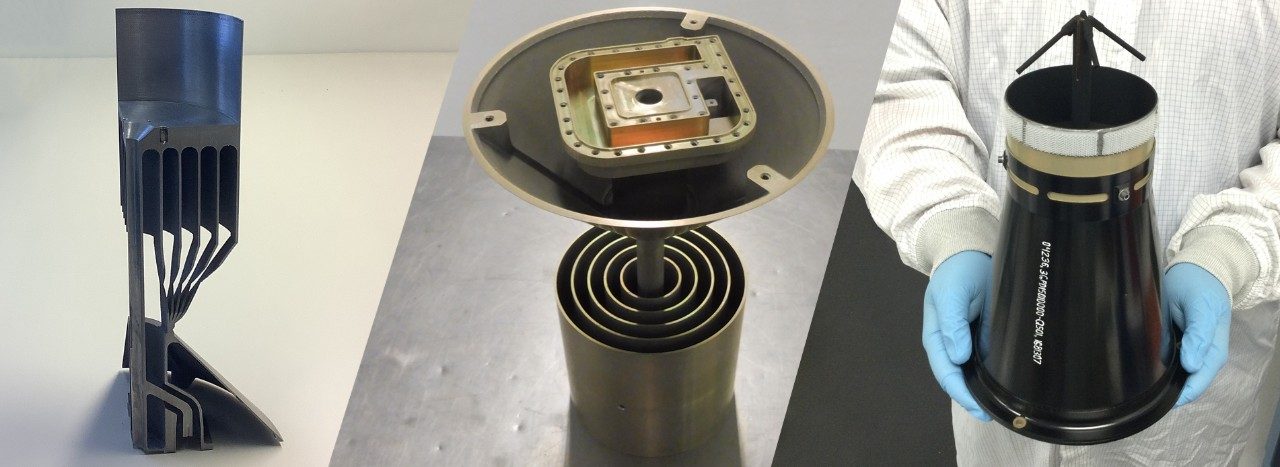
The Aerospace-developed space qualification process and guidelines have since been adopted by the contractor, and Aerospace has made these 3D-printing standards available to the broader industry to support future adoption by other space systems in the interest of advancing a more resilient and adaptable space enterprise.
“Despite there being no guidebook or published standard, Aerospace was walking down the path alongside the contractor every step of the way,” said David B. Witkin, Senior Scientist at the Materials Science Department. “Our experience enabled us not only to evaluate the contractor’s internal documents, but also to anticipate potential risks that the contractor may not have been aware of. So, in addition to providing the contractor with insights, we were also providing guardrails.”
With 3D printing showing promise as a viable means of producing satellite instrumentation, research is currently underway to assess the viability of the technology to produce the primary structures of satellites themselves. Earlier this year, Aerospace participated in tests associated with the qualification/proto-qualification of various items in the GPS IIIF solar array wing assembly, for which Aerospace's observations and methodology are to be incorporated into the guidance for the development of future 3D-printed designs.

Keeping pace with the rapid and continuous technological shifts that are reshaping space requires new approaches and ways of thinking. As evidenced by the use of 3D printing in component manufacturing, the application of new and evolving technology to national security space architectures exemplifies Aerospace’s ongoing efforts to advance the principles of Continuous Production Agility, which contributes to ensuring the space enterprise is well positioned to maintain leadership in this modern environment.
“There’s frequently an element of risk with new technology,” said Jung. “Qualifying the 3D-printed GPS III components also enabled us to set the standard for that qualification process, which will yield dividends down the road. Aerospace is uniquely positioned to assist the customer and contractor with new technology insertion because we have so much experience to draw from.”