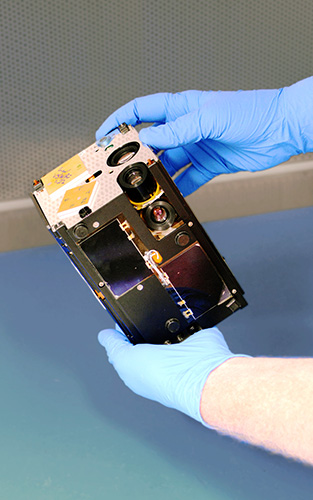
Ideally, every critical mechanism on a spacecraft is thoroughly tested before flight. In practice, that’s not always possible, especially for CubeSats and other small spacecraft. For example, many satellites employ an actuating mechanism known as a “meltwire”, which uses an electrically heated wire or resistor to melt through a restraining element, thereby releasing a deployable element such as a solar array or instrument boom. Thanks to their low development cost and simplicity, they are commonly used on small spacecraft, but present some significant drawbacks. By design, they can only be used once, which means that the actual flight unit cannot be tested before flight. As a result, developers must spend a considerable amount of time and expense to repeat the actuation tests enough to ensure reliability. This can lead to undertesting.
Improving Reliability With Shape-Memory Alloys
Jerry Fuller of Small Satellite Development and Operations has been investigating reliable alternatives to meltwires, particularly for small satellites. His current research has focused on the use of shape-memory alloys such as nickel-titanium (nitinol). These materials can change shape in response to a change in temperature, which makes them potentially quite useful for applications requiring precise and reliable movement. Moreover, they can be used and reset many times, so the actual flight article can be the one that gets tested.
Understanding The Physics Of Failure
Nitinol actuators for spacecraft are not new, but they have been largely overlooked by the CubeSat community despite their unique benefits. For example, these mechanisms can be designed to be “nearly two-dimensional,” Fuller says, which should make them highly desirable for applications that can’t afford much mass or volume.
Fuller is exploring various design options. The most basic approach replaces the meltwire with a length of nitinol wire. When heated (by means of an electrical current), the wire contracts, removing a restraint. This approach exploits an unusual property of nitinol: it can be made to shrink, rather than expand, when heated.
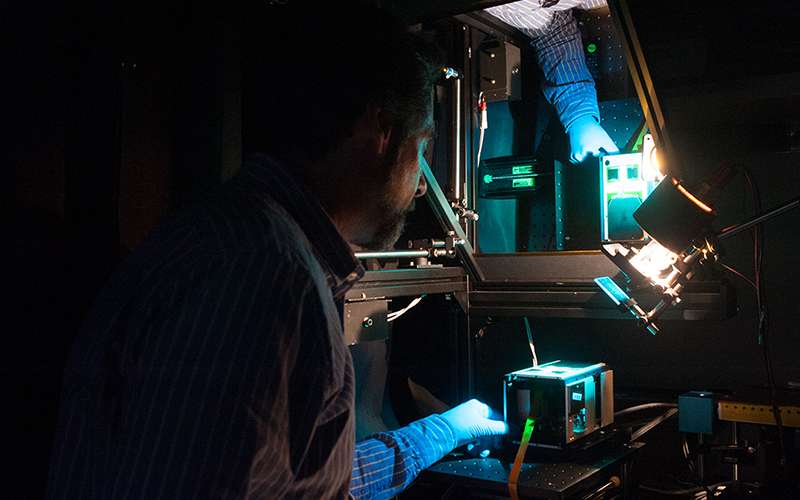
To create such a mechanism, Fuller says, a length of wire is “trained” during fabrication to be a certain length. “If you stretch it a little bit, then heat it up (usually to about 90 degrees Celsius), it will contract to its original, trained, length.” The trick, he says, is to design a mechanism that can reliably take advantage of that small, precise contraction to do something useful. “Generally, this means mechanisms that are over an inch in length.” Typical designs involve “tiny wires, about six thousandths of an inch in diameter,” he says. These wires can deliver a pull force greater than a Newton (about a quarter of a pound).
Many of these mechanisms also take advantage of the “superelastic” properties of nitinol. “We often use superelastic nitinol in place of a steel spring,” Fuller explains. “You can bend it more sharply before it exceeds its elastic limit.”
The Future Of Space Materials
Actuators made from shape-memory alloys have flown on several CubeSats built by Aerospace and are scheduled to fly on upcoming missions as well. There are even commercial off-the-shelf units on the market. The devices are well suited to space applications, as they are light and simple and can be employed in tight spaces. Even on large spacecraft, these small actuators can play a useful role. They can often be designed without lubrication, and they don’t suffer from residual magnetism (as electric motors or solenoids do). They can be tested and reset with ease and can often be adapted to new situations where other devices wouldn’t fit. “We’ve used shape-memory wire actuators to release solar arrays, deorbit-drag devices, antennas…Virtually any one-time-use actuator can be designed as a shape-memory wire actuator,” Fuller says.
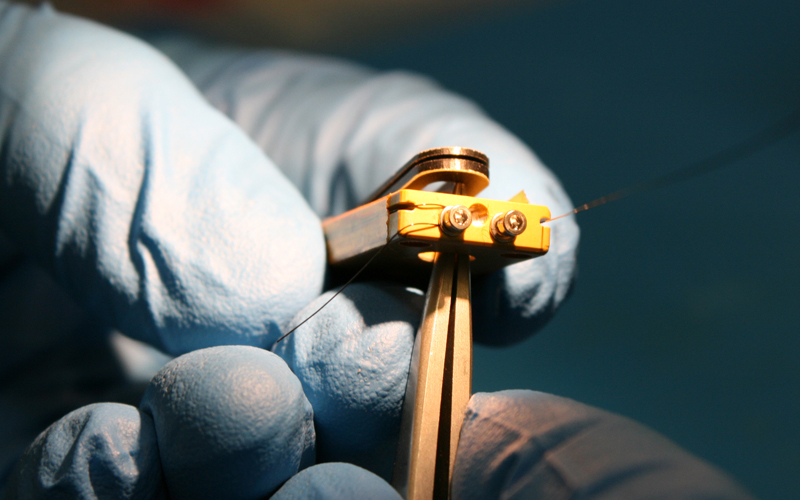
Although Fuller has been focusing mostly on CubeSats, actuators made from shape-memory alloys will ultimately improve the reliability of spacecraft across a range of mass classes. “Shape-memory actuators will allow developers to build mechanisms that deploy antennas, solar arrays, or instruments that can be tested much more conveniently than other release devices that must be replaced with each test,” he said.